Leading a Year-Long Space Microgravity Design Team
Tl:dr; Engineering design teams are loads of fun but tough to execute. Had opportunity to co-found and lead Waterloo Space Soldering design team and run the experiment flying in microgravity.
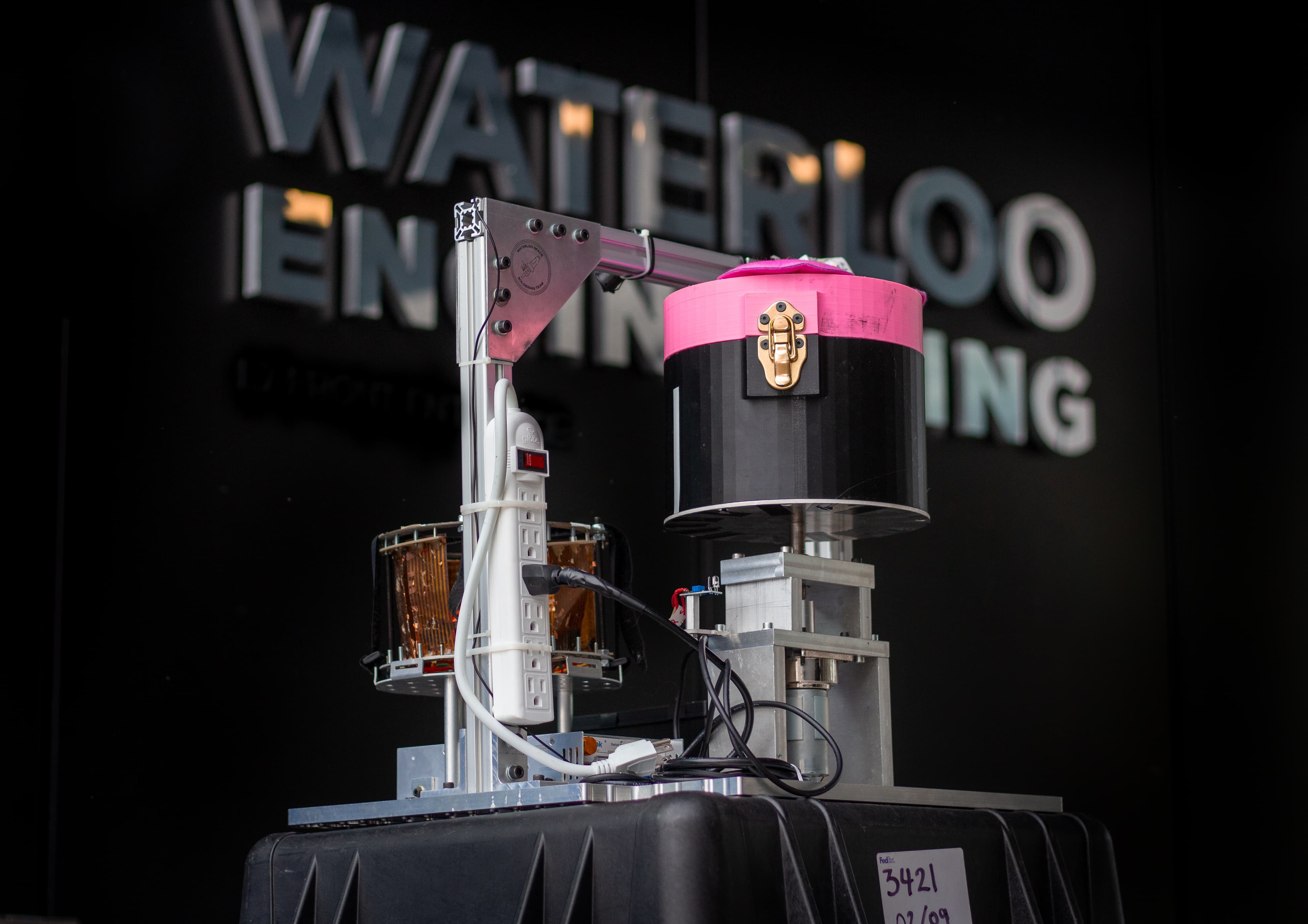
Photo I took of final assembly. Very happy how it turned out.
Navigating the Rapids: Engineering a Complex System Under a Tight Deadline
Our recent project was a masterclass in compressed design cycles and the art of rapid engineering. We embarked on this journey with an extraordinarily tight timeline, demanding decisive action and a laser focus on efficiency. The project's integration into the MTE380 course, tying its success to academic performance, proved to be a catalyst, driving rapid progress and focused decision-making. We had 2 months to build a proposal and when it got approved, we had less than 8 months to design, build, and test it.
Preface to this Experience: My Year in the Mars Rover Robotics Design Team
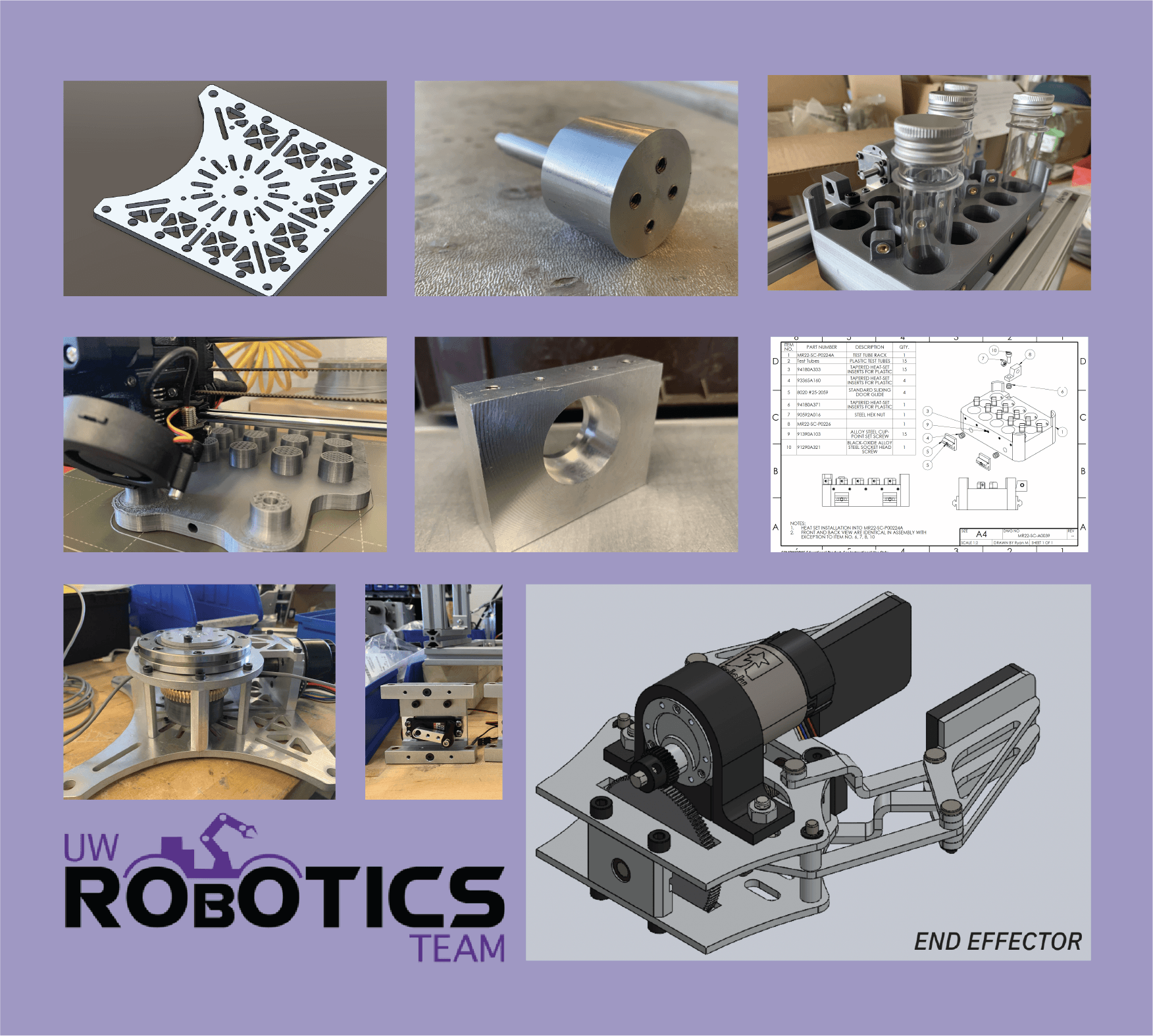
Some designs and parts I manufactured for the robotic arm
In 2022, I was a member of the mechanical design team for a year, which was an incredible experience in terms of building and creating. Mechanical Team designs and manufactures parts for the UW Mars Rover robotics team. It was awesome buying some beautiful gear motors, manufacturing parts, and developing designs. However, the most disappointing part was not being able to integrate fully with the team and witnessing its internal collapse.
Unfortunately, we didn’t make it into the competition, and the lack of coordination among the subteams was catastrophic. Two years later, the team has still not fully recovered.
It is through learning the engineering excellence from the team but also some structural challenges, that I carried into the new team.
The Foundation: Principles for Rapid Development
Several core principles formed the bedrock of our approach:
- Regular Iterations: Recognizing the inherent limitations of an abbreviated design cycle, we embraced iterative engineering. This allowed us to quickly test and refine concepts, preventing scope creep and propelling the project forward.
- Interconnected Systems: We prioritized close collaboration between teams from the outset, breaking down silos and fostering a holistic approach. This ensured seamless integration and minimized potential conflicts.
- Murphy's Law Mitigation: Acknowledging the inevitability of unforeseen challenges, we prioritized early action to mitigate risks. This proactive approach allowed us to address potential issues before they escalated.
Proof of Concept: Rapid Validation
A critical early step was the rapid validation of our core concept. We needed a method to achieve a specific outcome within a stringent 20-second timeframe. Radiation was quickly ruled out, leaving us to explore conduction and convection. While the concept of a larger, oven-like system was initially considered, it was deemed impractical.
To demonstrate the fundamental dynamics of our system, we developed a proof-of-concept using a motor and wheel. This allowed us to visualize the effects of rotation and identify potential challenges. Eccentric loading emerged as a significant hurdle, highlighting the need for careful balancing and control.
The Classic Murphy's Law Story
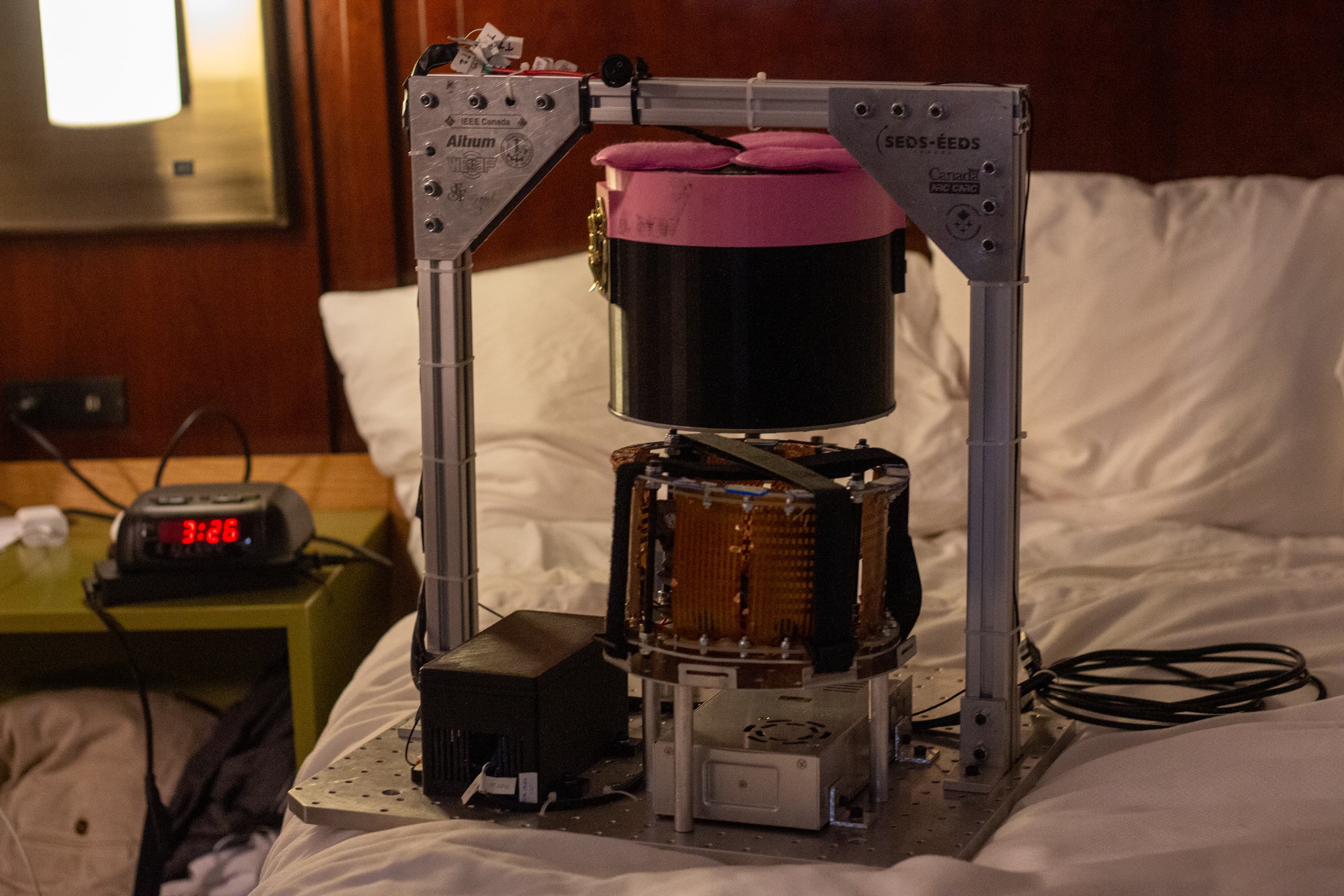
Something always done last minute. In our case, the wire mapping was not done right so we had to cut all the wires, remap, and solder all of the wires before the first flight in the morning. Nathan, Rejia, Andre, and I were surprised but realized the job needed to be done so we did it and finished at 3 am.
The Manufacturing Gauntlet: Lessons Learned
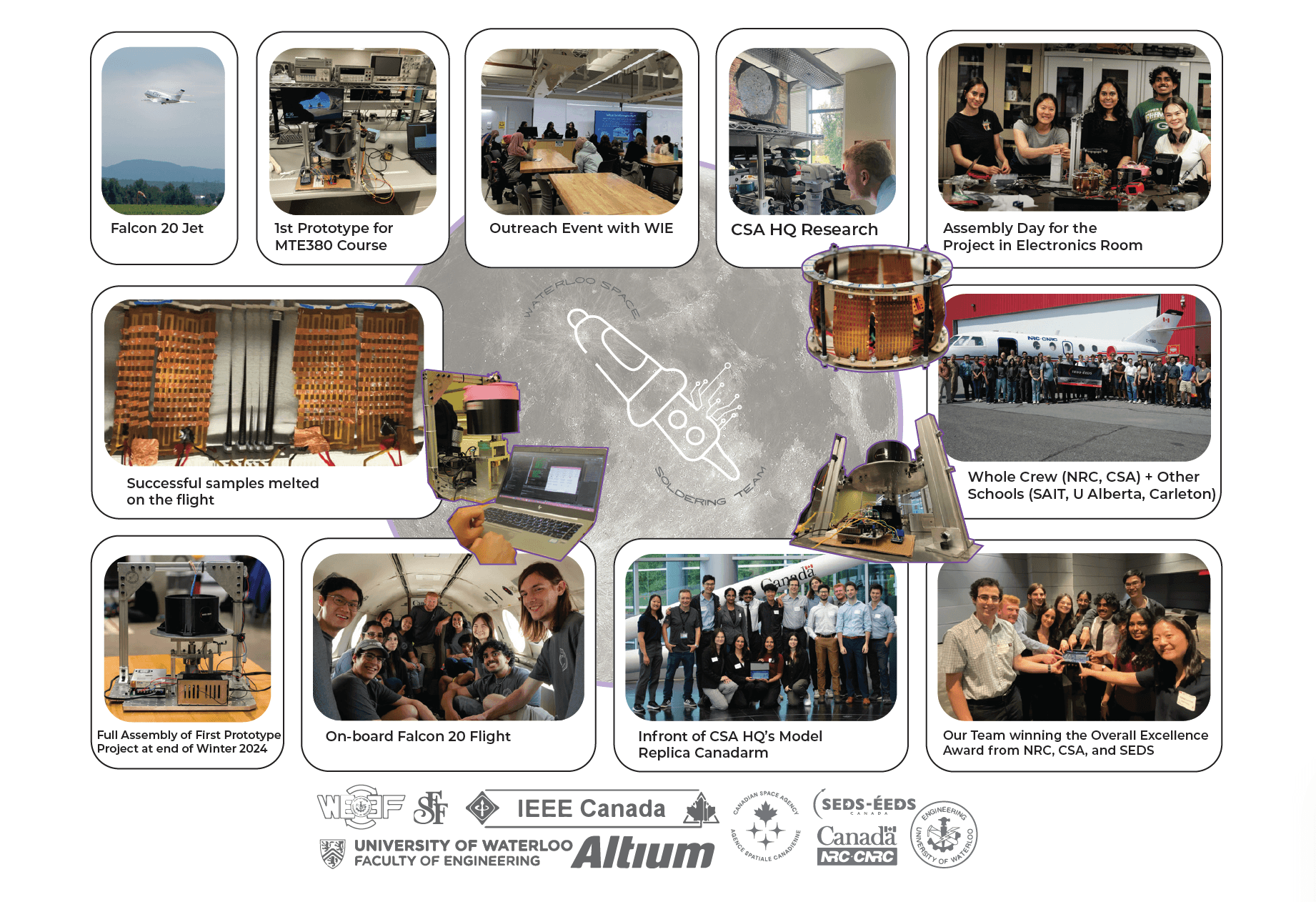
Collection at moments and designs that were done for the project
The final manufacturing phase was a crucible, revealing critical areas for improvement:
- Material Selection and Manufacturing: The fragility of 3D-printed components and the efficiency of waterjet cutting became evident. We learned the importance of matching materials and manufacturing processes to the specific requirements of each component. Additionally, the rigidity of steel over aluminum became a valuable lesson.
- Assembly and Verification: Challenges with snap ring detachment and electrical tape adhesion underscored the need for robust assembly procedures. Implementing a double-verification process for mechanical torque proved essential for ensuring secure fastenings.
- System Dynamics and Control: The behavior of airflow through NACA ducts at high speeds revealed the importance of comprehensive system characterization. Integrating sensors and automation into the control system was identified as a key area for future improvement.
- Timeline and Planning: Manufacturing components in the final week resulted in insufficient buffer time. We realized the importance of initiating manufacturing earlier in the project timeline.
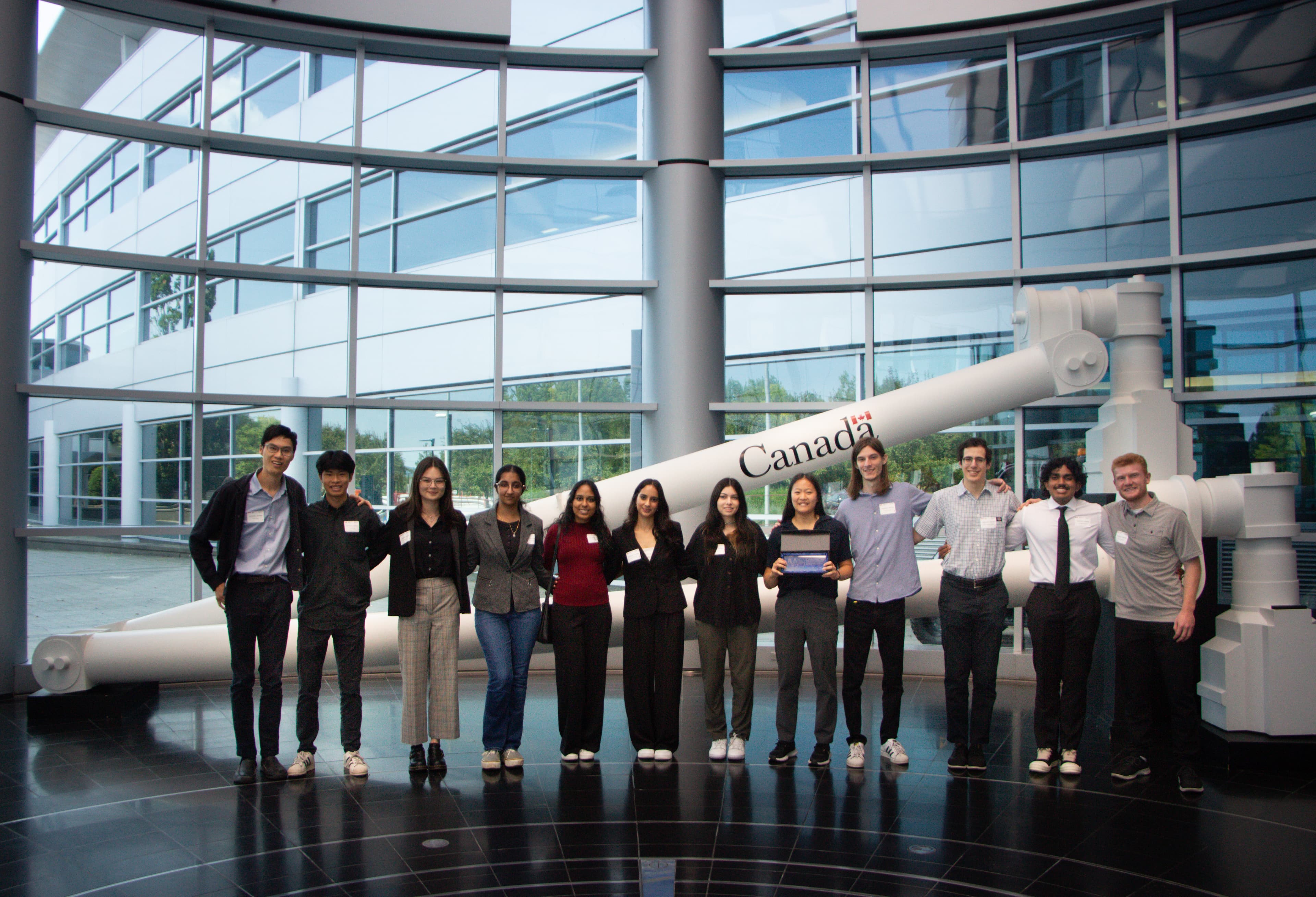
Photo outside the Canadian Space Agency Headquarters in Montrael
Key Takeaways:
- A compressed design cycle demands rigorous scope management and a proactive approach to risk mitigation.
- Iterative engineering and close team collaboration are essential for rapid development.
- Thorough system characterization and testing are crucial for achieving optimal performance.
- Material selection and manufacturing processes must be carefully evaluated to ensure component integrity.
- Proactive planning, early manufacturing and standardized verification processes improve the quality of the final product.
This project provided invaluable insights into the challenges and rewards of engineering under pressure. By applying the lessons learned, we can improve our processes and achieve greater success in future endeavors.